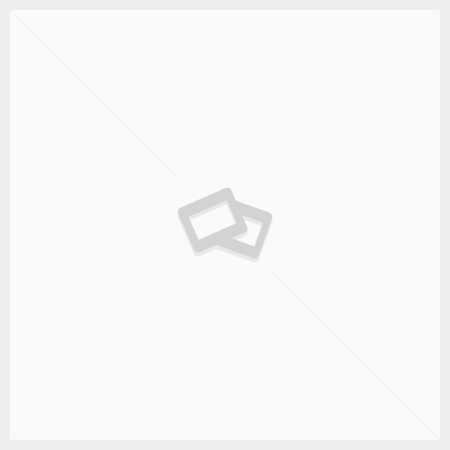
What is a Joint Cost? Definition, Methods, Examples, Joint Products
Companies normally use common costing information in managerial decisions, but this type of cost tracking is particularly useful for external accountants. Production costs remain universal, or common, until a split-off point where the product undergoes different processes. For example, an entire field of corn costs the same to grow, but after harvest and distribution these processes change when half is prepared as popcorn and the other designated as corn flour. At first the single product had a common cost, then at the split-off point, the two products’ costs began to differ. The cost allocations are entirely different between the two allocation methods, since the first calculation is based on revenue at the split-off point, and the second is largely based on costs incurred after the split-off point. The cost of raising livestock to the point of butchering can be considered a joint cost.
Accounting for Joint Costs
If the company is issuing GAAP based financial statements, on the other hand, the joint costs must be allocated to the products or departments benefiting from the costs either on a physical basis or a value basis. Most of the time a physical basis is used to allocate joint costs because it is less subjective than the value basis. Accounting attributes common costs to all production departments since these costs cannot be assigned to any specific area.
The quantity produced is 100Kg and 150Kg; and sold at ₹750 and ₹600 per Kg, respectively. If the estimated profit on sales is 50% on Sugar, 40% on Molasses and 34.27% on Jaggery, apportion the joint cost using reverse cost method. When we undergo the apportionment of joint cost for accounting purpose, we will see that there are different methods available for determining it.
Since the expense over raw material, labour and processing of such products are incurred as a collective cost. In this chapter, we learn about joint costs and how we can effectively manage and grow our business. In a single manufacturing process, multiple joints and by-products are generated. Accurate allocation and management of joint costs contribute to the strategic planning and financial health of a company. It provides valuable insights into which products are more profitable and which processes could be optimized for cost efficiency.
Accurate allocation and analysis of these costs play a critical role what is a perpetual inventory system in pricing, profitability analysis, cost control, and strategic decision-making. While joint costs and common costs may, on the surface, appear very similar, they have a very different meaning in business accounting. Joint costs arise when the same resource results in two or more different products at the same time.
At the split-point, we have option to sell both products or processes further for more revenue. In dairy products, the skimming of raw milk yields skimmed milk, cream and did you have any interest or dividend income butter. Also, in the case of processing coconut, we get coconut water, coconut cream, desiccated coconut and jute. You can change your settings at any time, including withdrawing your consent, by using the toggles on the Cookie Policy, or by clicking on the manage consent button at the bottom of the screen. It also helps to set the point on the products according to their economic value.
The Tax Calendar 2024 provides a roadmap for individuals and businesses, highlighting key dates and actions mandated by federal tax laws, to ensure compliance and financial efficiency. They turned 100 gallons of petroleum into 38 gallons of gasoline, 35 gallons of diesel, and 27 gallons of crude oil. Some costs are specific to the services, for instance, meals and flight attendants are specific costs of carrying passengers. It is in their very nature that Joint products or By-products can’t be produced individually.
- Under the contribution margin method, the joint cost apportionment is done through marginal costing technique where the contribution can be understood as the surplus of sales over the variable cost.
- When we undergo the apportionment of joint cost for accounting purpose, we will see that there are different methods available for determining it.
- For that, a new form of cost allocation is available, which is double or multiple allocations.
- Key features like real-time reporting, customizable dashboards, and mobile access help businesses stay agile and competitive.
Absorption Costing: Definition, Formula, Calculation, and Example
It is the cost accountant’s job to trace these costs back to a certain product or process (cost object) during production. Some costs benefit more than one product or process in the manufacturing process. These methods are mainly classified onto engineering and non-engineering methods. Nonengineering methods are mainly based on the market share of the product; the higher market share, the higher proportion assigned to it e.g. net realizable value. In this method, the proportions are determined based on the sales value proportions.
Examples of Joint Cost Allocations
The butchering process yields multiple products such as meat cuts, hides, and by-products used for manufacturing cosmetics and pharmaceuticals. Identifying and allocating the costs to each of these products can only effectively take place after the butchering process, which serves as the split-off point. Joint cost is an effective accounting procedure to determine the individual cost of those products which are produced or extracted together. It is the basis of individual price ascertainment of the joint products.
This complexity underscores the importance of using consistent and logical methods to ensure the reliability of cost information for decision-making purposes. The physical units method is usually applied to the joint products which are similar in state and have a standard unit of measurement. In this method, the apportionment of the joint cost is done through relative quantity or weight of the joint products, at the split-off-point.
It is a way to create a healthy work environment in organizations and have the plans and strategies to succeed.
By-products are secondary products that have less commercial value compared to the main products. While joint costs are allocated to the main products, by-products are often accounted for separately, sometimes even credited against the joint costs to reduce the total cost attributed to the main products. The method chosen depends on the nature of the products and the information available at the split-off point.
Joint Cost allocation
While manufacturing, there comes the point where those yielded products get differentiated from each other. Joint cost allocation has advantages for a growing company, but it may also get difficult. The net realizable value method will take into account both sale and the additional cost require to complete the product.
A joint cost is an expenditure that benefits more than one product, and for which it is not possible to separate the contribution to each product. These expenditures can include direct materials, direct labor, and factory overhead. Moreover, the variable cost is determined with the help of units sold, and the fixed cost is ascertained through the contribution margin ratio. However, there is no formal logic for adopting a particular method of apportionment. An organization can opt for any of the methods available, depending upon the business type, uniformity of products, etc. This helps calculate the total cost price and selling price of those products and conjecture the profit overall.