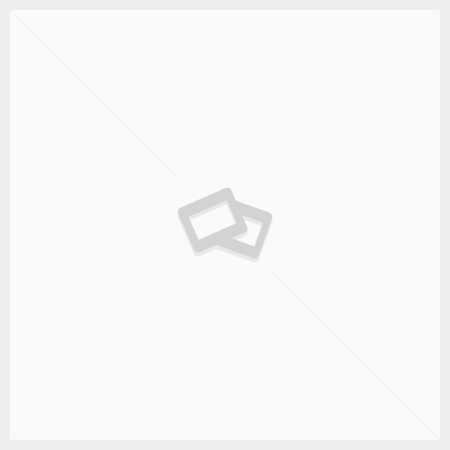
Joint Cost Example Allocation
The expense incurred by producers when creating more than one product or process is referred to as the joint cost. These costs include labor, materials, and overhead for the joint product’s manufacture. Almost every manufacturer uses joint cost allocation to keep input costs under control. The costs allocated to joint products and by-products should have no bearing on the pricing of these products, since the costs have no relationship to the value of the items sold. Prior to the split-off point, all costs incurred are sunk costs, and as such have no bearing on any future decisions – such as the price of a what is black friday product.
Typical universal costs in small businesses include electrical expenses, transportation and money costs such as depreciation and income taxes, reports Send Pulse. These shared costs include the basic production of multiple goods, and fuel costs. Some common costs change according to increases or decreases in overall production.
Often times manufacturers will ship a product to customers with advertisements or catalogs in the package. The shipping cost benefits both the product as well as the advertising campaign. Even though the cost of shipping the catalog might be insignificant compared to the cost of shipping the product, the cost is still shared between the two departments. The products can be further processed as per convenience or can be sold after reaching the Split-off point. The cost that has incurred up to the Split-off point is called Joint Cost. Given the immateriality of by-product revenues and costs, byproduct accounting tends to be a minor issue.
Methods of Apportionment of Joint Cost
Common costs are harder to identify, but include all costs that keep the business running but which cannot be attributed to one product, department, project, territory or other specific cost center. Understanding the full scope of such concepts helps accountants and managers know which departments to charge for incoming costs. The accountant needs to determine a consistent method for allocating joint costs to products. This means identifying the products to which joint costs will be assigned as soon as they are separately identifiable in the production process (known as the split-off point). Joint costs pertain to the shared costs of producing main products up to the split-off point.
Why Joint Costs Matter
The situation is quite different for any costs incurred from the split-off point onward. Since these costs can be attributed to specific products, you should never set a product price to be at or below the total understanding current assets on the balance sheet costs incurred after the split-off point. Under the contribution margin method, the joint cost apportionment is done through marginal costing technique where the contribution can be understood as the surplus of sales over the variable cost. Joint costing becomes useful when expenses simultaneously benefit two or more departments of a business. Special numbers or attribution in accounting indicates the cost is a joint cost. As such, the accounting department assigns the cost twice in the appropriate proportion to the corresponding departments.
In the engineering based method, proportions are found based on physical quantities and measurements such as volume, weight, etc. One of the simplest methods to apportion joint cost is the average unit cost method. Here, the average cost per unit is calculated by simply dividing the total cost of all the joint products incurred before their splitting-off, by the total of the number of units produced all together. Joint costs refer to the costs incurred during the production process that are attributable to two or more products simultaneously. These are common in processes that yield multiple end-products from a single input or series of processes.
By-product costing and joint product costing
The company needs to allocate all the costs to each product type in order to set the price and calculate its profitability and prepare a proper business plan. Globe Oil Ltd., a petroleum extradition firm, is a market leader in the petrol, diesel, and crude oil domains. They needed to know the cost of production for each of their products because their base product is the conduit through which all other by-products are exported. A cashew nuts processing unit produces two varieties of cashew nuts, premium and regular, at a joint cost of ₹75000, out of which ₹25000 is the fixed cost.
The refinery process converts crude oil into several different products such as gasoline, diesel fuel, asphalt base, heating oil, kerosene, and liquefied petroleum gas. The costs of refining crude oil—such as labor, utilities, and depreciation on the refinery equipment—are incurred to produce all these products simultaneously until the split-off point is reached. Only after this point can the refined products be identified and measured independently. Thus, all costs incurred before the split-off point are considered joint costs. The estimation of the individual cost (usually direct cost) involved in the manufacturing or extraction of joint products is a complicated task.
- It provides valuable insights into which products are more profitable and which processes could be optimized for cost efficiency.
- Only after this point can the refined products be identified and measured independently.
- The refinery process converts crude oil into several different products such as gasoline, diesel fuel, asphalt base, heating oil, kerosene, and liquefied petroleum gas.
Joint costing makes a useful tool for encouraging budgeting cooperation between departments. It’s not always possible to separate the cost or contribution between the beneficiaries accurately, but joint costing is an acceptable form of accounting for most small businesses. Common costs are general, not attributable to any one department or area of the small business.
A joint cost is a kind of common cost that occurs after a raw product, such as a sunflower crop, undergoes two separate production processes, reports Strategic CFO. For example, the cost of fertilizing and harvesting sunflowers qualifies as a common cost. If a company uses the kernels in two or more different processes – such as roasting and crushing – the costs become joint costs. In the end, you’ll have two different kinds of products but with similar shared costing until a split-off point. It is the cost accountant’s job to trace these costs back to a certain product or process (cost object) during production. Almost all manufacturers incur joint costs at some level the manufacturing process.
Allocating joint costs presents several challenges due to its subjective nature. Choosing an allocation base that fairly distributes the costs among products can be difficult, especially when the physical attributes or market values of the products vary significantly. Moreover, the allocation process can be complicated and may require estimates and assumptions, which introduces a margin of error.
In many industries, a common manufacturing process generates multiple products, such products derived by this process are called Joint products or By-products. This method is applicable to the output that can be separated from each other, the final products have a similar state with the standard of measurement. This method will measure the products at the split-off point base on their quantity or weight.
Joint cost is the cost that incurs during the production of multiple products at the same time. The production requires similar raw material, but result in multiple products type. We will not be able to separate the joint cost until the split-off point. Understanding and managing joint costs is essential for businesses that produce multiple products from a single process.