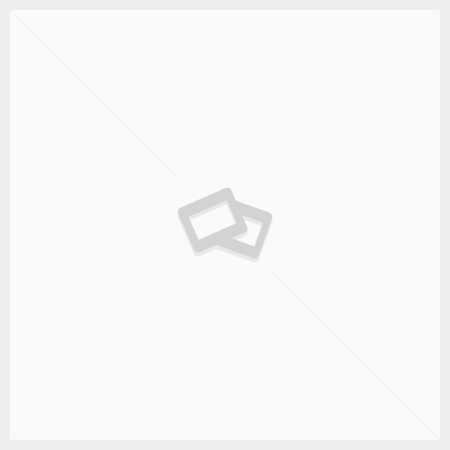
Activity Cost Driver: Definition and Examples
For example, under ABC, a manufacturing company may decide to allocate rent expense to each product based on the amount of space the machines that are utilized to produce that particular product uses. In ABC, an activity cost driver influences the costs of labor, maintenance, or other variable costs. Cost drivers are essential in ABC, a branch of managerial accounting that allocates the indirect costs, or overheads, of an activity. By using the activity cost driver (labor hours), XYZ Manufacturing can allocate its assembly cost more accurately to each product, helping the company make better decisions about pricing, resource allocation, and process improvements. By updating the ABC model on the basis of events rather than on the calendar (once a quarter or annually), you get a much more accurate reflection of current conditions. And any time they learn of a significant and permanent shift in the efficiency with which an activity is performed, they update the unit time estimate.
football jerseys
Nike Air Max 270 white
nike air max womens
Jerseys for Sale
nike air jordan sneakers
nike air jordan shoes
nike air jordan 1
best couples sex toys
adidas promo code
nike air max for sale
custom baseball jerseys
custom football jerseys
custom hockey uniforms
- Rather than attempt to downsize the plant, he decided to maintain the capacity for a large contract he expected to win later that year, for which he otherwise would have created new capacity.
- Time equations greatly simplify the estimating process and produce a far more accurate cost model than would be possible using traditional ABC techniques.
- Such expansion has caused ABC systems to exceed the capacity of generic spreadsheet tools, such as Microsoft Excel, and even many ABC software packages.
- The ultimate goal is to maximize profits; a key way to accomplish this is by being aware of all expenses and keeping them in check.
- Let’s say employees report that they spend (or expect to spend) about 70% of their time on customer orders, 10% on inquiries or complaints, and 20% on credit checks.
- Setting up machines for a new product would need 400 setups and overhead of $800,000.
- Most have reported substantial improvements in profitability that they attribute to the information generated by the new approach.
A cost driver for the painting department might be the increased wages in accordance with the new union agreement. Since preparing car bodies is a fairly labor intensive operation, an increase in wages can drastically increase the cost of the activity. Accountants who estimate cost drivers must possess a thorough understanding of what goes into the production of a particular good or service.
Example of an Activity Cost Driver
Over the past seven years, we and our colleagues at Acorn Systems have successfully helped more than 100 clients introduce time-driven ABC into their processes. Most have reported substantial improvements in profitability that they attribute to the information generated by the new approach. Take the case of Banta Foods, a Midwest food distributor with revenues of $155 million from 17,000 SKUs and 5,000 customers. Historically, its profit drivers were increasing the number of orders taken per day, increasing aggregate revenues, and controlling aggregate expenses.
For this reason, the selection of accurate cost drivers has a direct impact on the profitability and operations of an entity. A cost driver is defined as a unit of activity that causes a business Activity Cost Driver to endure costs. The extra time for changeovers to clean out allergens (such as nuts, eggs, soy, or wheat) used in certain ice cream products could now be accurately assigned to those products.
What Do You Mean by Cost Driver?
There are no industry standards stipulating or mandating cost driver selection. Company management selects cost drivers based on the variables of the expenses incurred during production. Examining activity cost drivers helps companies to reduce unnecessary expenses and get to grips with how much an order really costs. The ultimate goal is to maximize profits; a key way to accomplish this is by being aware of all expenses and keeping them in check. When a factory machine requires periodic maintenance, the cost of the maintenance is allocated to the products produced by the machine. Therefore, every machine hour results in a 50-cent (500 / 1,000) maintenance cost allocated to the product being manufactured based on the cost driver of machine hours.
What is activity cost driver and resource cost driver?
Resource cost Driver is measure of quantity of resources consumed by an activity. It is used to assign cost of a resource to activity or cost pool. Activity Cost Driver is measure of frequency and intensity of demand placed on activities by cost object. It is used to assign activity costs to cost objects.
Notice how the total overhead for the month of January is the same at $200,000 but the amount allocated to each product is different. The key insight is that although transactions can easily become complicated, managers can usually identify what makes them complicated. The variables that affect most such activities can often be precisely specified and are typically already recorded in a company’s information systems. To take an example, let’s assume a manager is looking at the process of packaging a chemical for shipment.
How Activity Cost Drivers Work
The application rates are $1,250 for each product design, $50 per order, $1.25 per direct labor hour, and $1,000 per customer. Time-based cost drivers use the length of time it takes to complete an activity for allocating production overhead costs. This type of cost driver can use different types of labor hours to allocate overhead costs. First, the time it takes to set up a production run or retool machines may be one type of time-based cost driver. Second, the number of direct labor hours used to produce one unit may also be a common type of driver.
They then determine a particular activity’s impact on the production of that product. Keeping tabs on cost drivers makes it easier to determine the actual cost of production and make more accurate financial projections. They are identified by identifying costs, investigating relationships and correlations between costs and activities, analyzing measures, and wrapping up by making sure the cost driver used is a good measure. https://kelleysbookkeeping.com/petty-cash-definition/ Cost drivers are used as the application base in calculating the application rate to be applied to a product’s cost. Cost drivers are important because they allow management to better understand the true costs by improving overhead allocation to their products. This formula applies to all indirect costs, whether manufacturing overhead, administrative costs, distribution costs, selling costs, or any other indirect cost.
Cost Drivers in Accounting Analysis & Examples
Or imagine the activities involved in making a complex product such as an automobile or computer. My Accounting Course is a world-class educational resource developed by experts to simplify accounting, finance, & investment analysis topics, so students and professionals can learn and propel their careers.